Ultrasonic-Sensing Bin
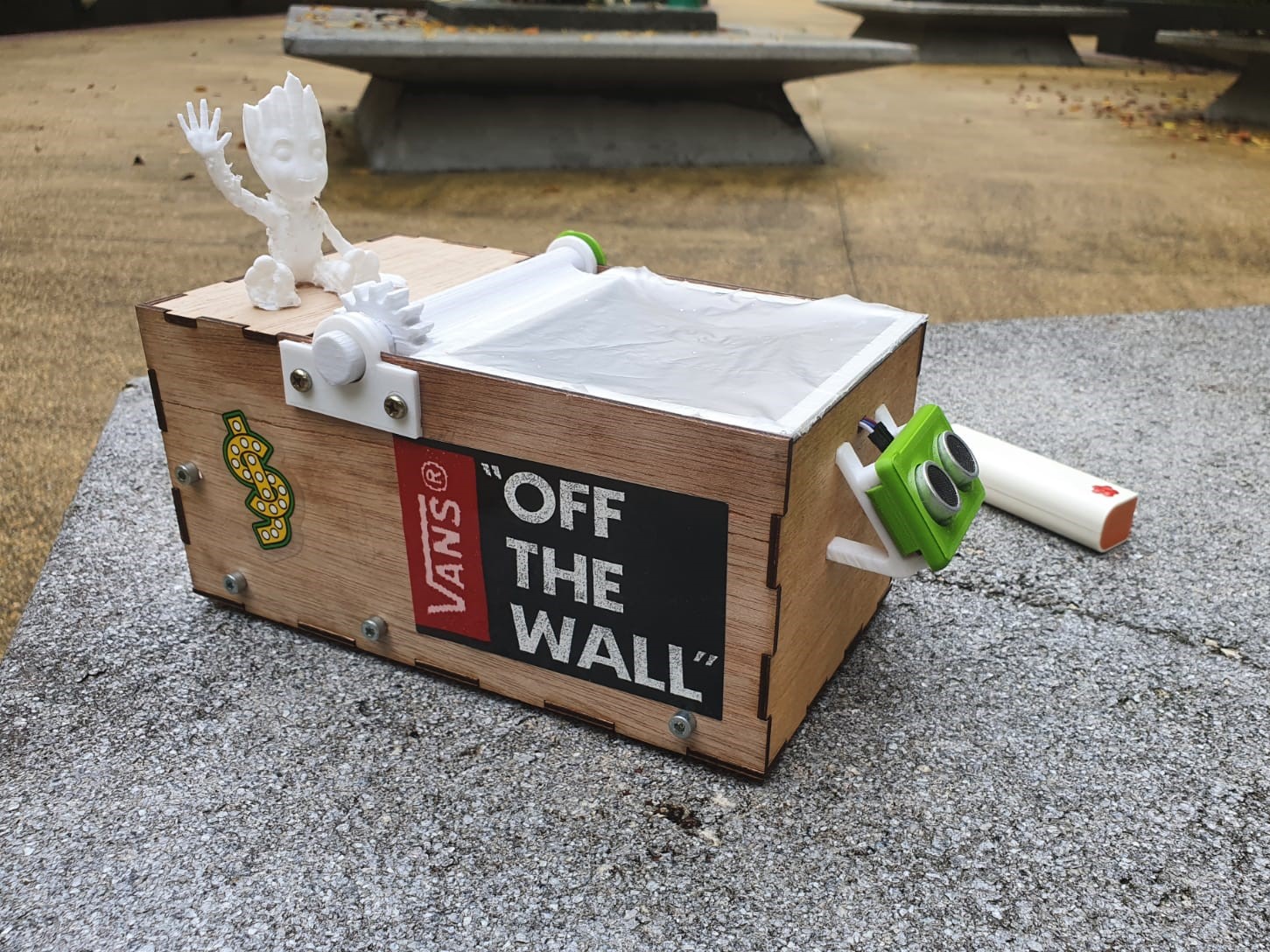
What inspired my idea?
At the time of making this project, we live in a world ravasged by the coronavirus. This project aims to reduce the contamination of bacteria in the environment by allowing users to throw in their rubish without contacting the bin. And the rubbish will also be enclosed so as to prevent scavenger animals from flocking to the rubbish bin.
Design of the Ultra Sonic Sensing Rubbish Bin
1. Housing (laser cut)
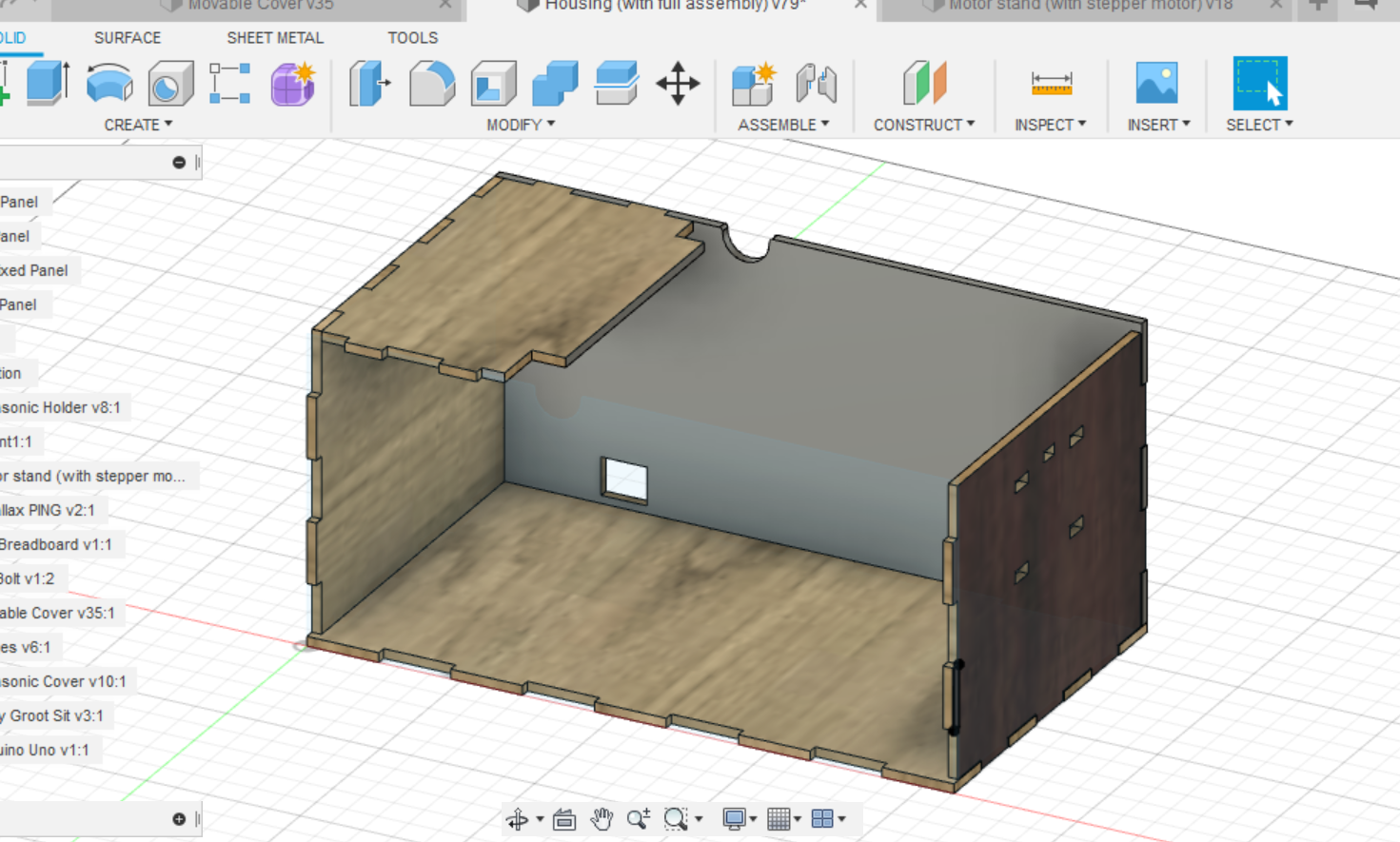
2. Movable Cover
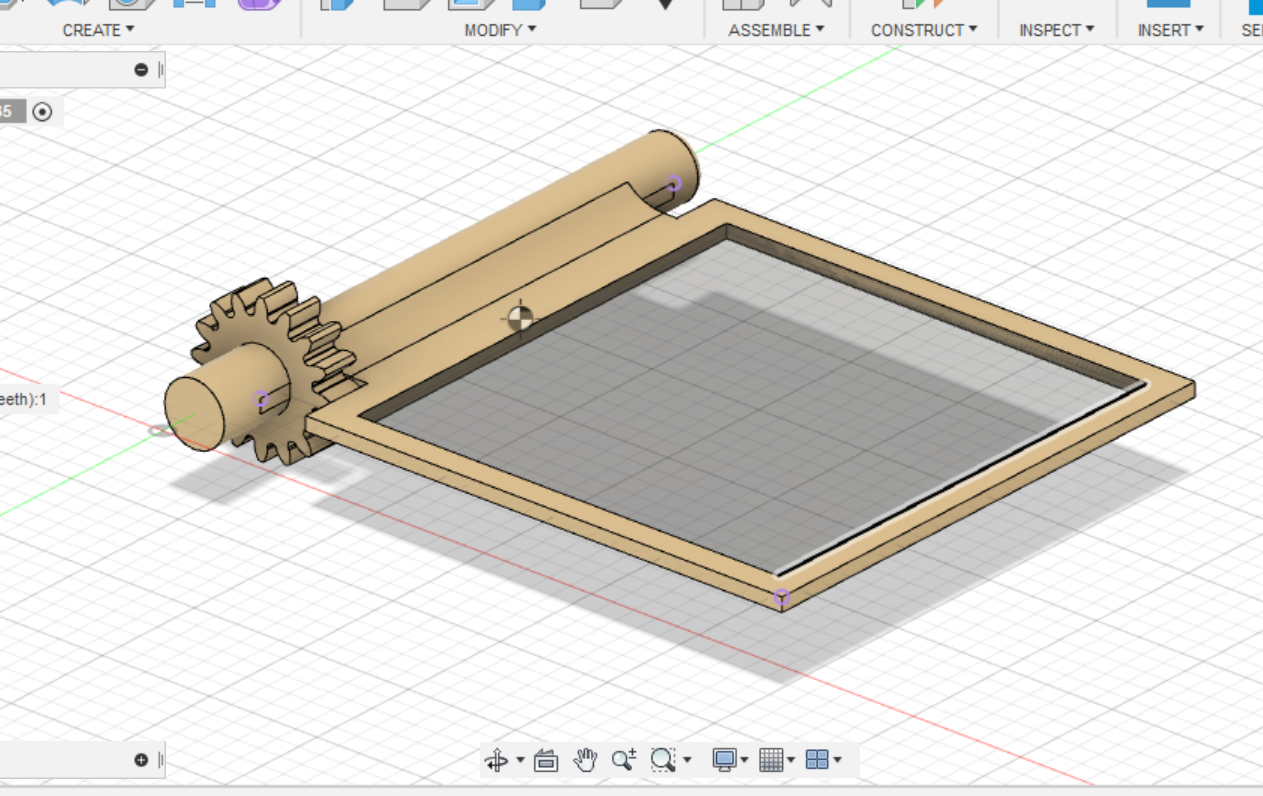
3. Hinges and Washers
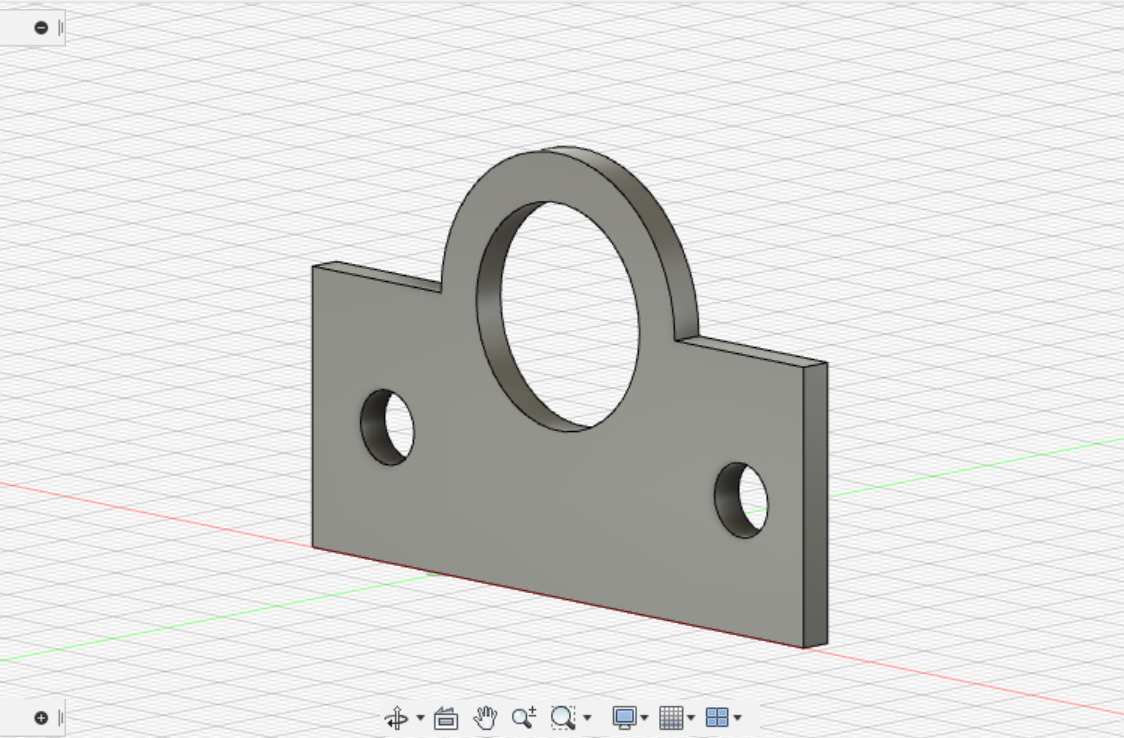
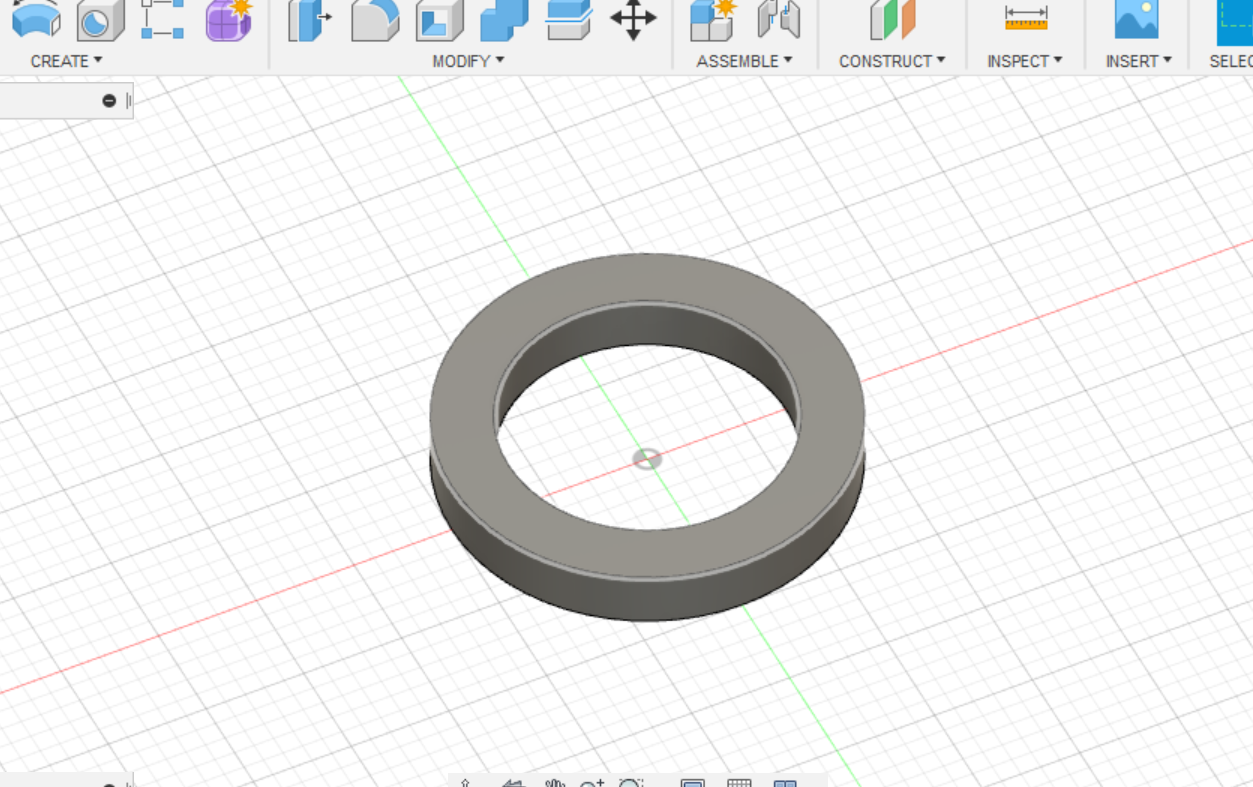
4. Ultra-sonic Sensor Section
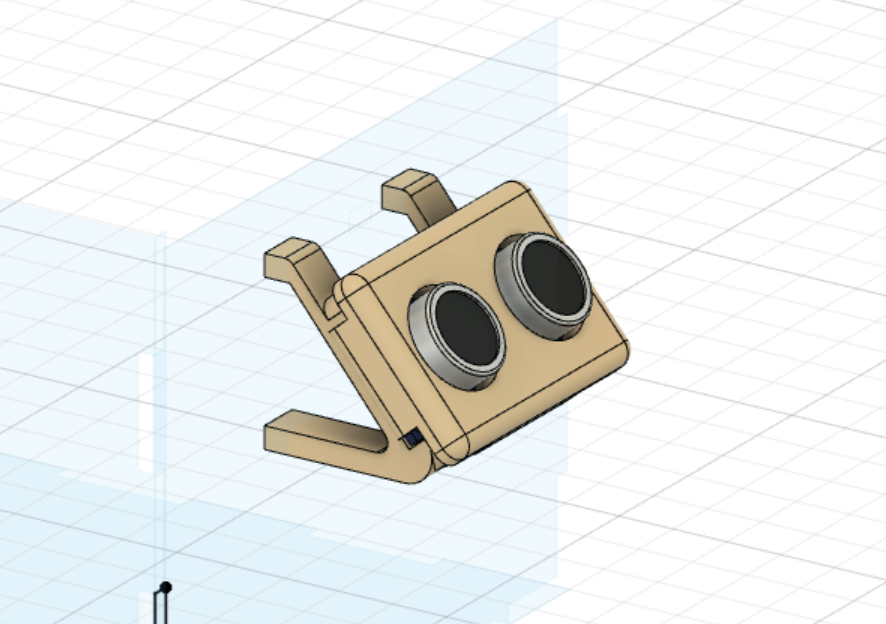
5. DC Motor Section
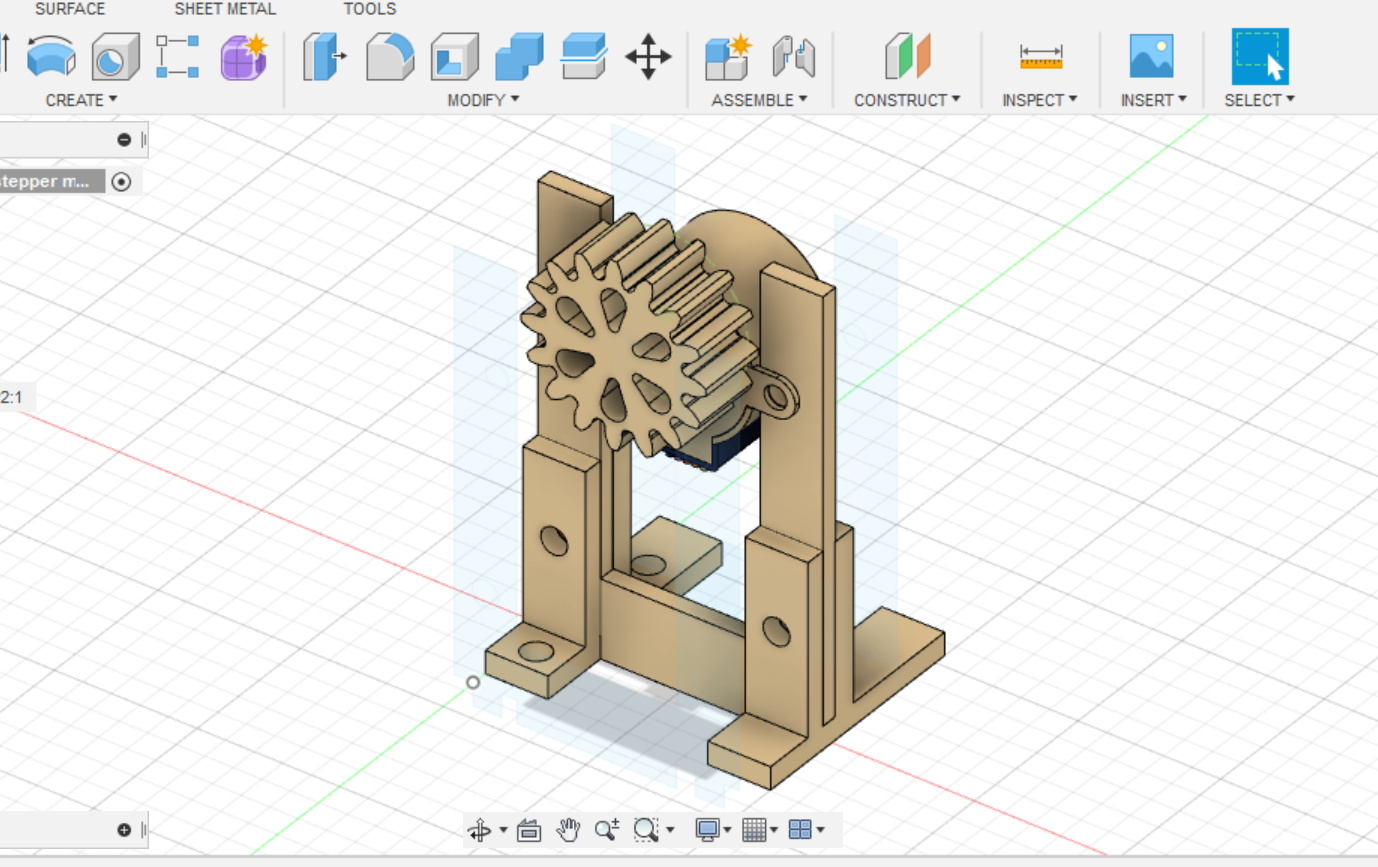
Circuit Simulation/Actual
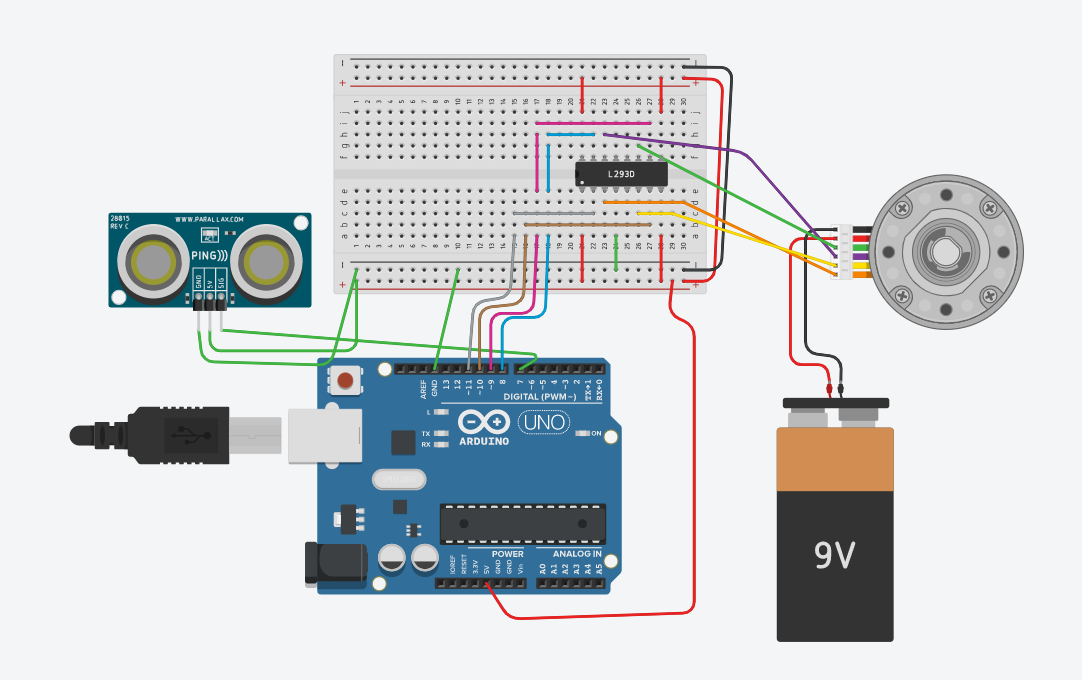
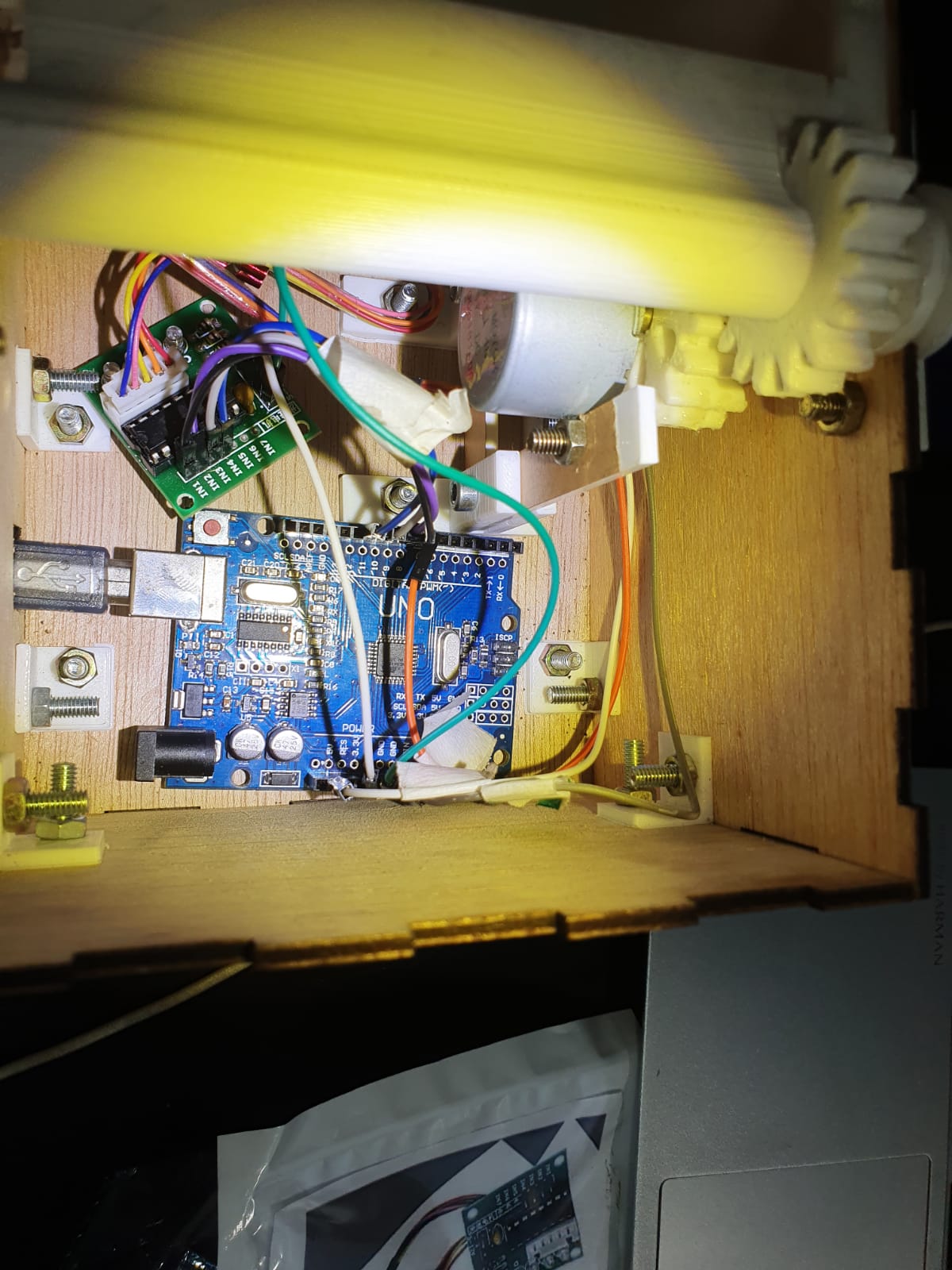
Download Project Code
Challenges/Issues
1. The first challenge I face was ensuring that the motor stand (vertical part) remained secured at a fixed 90 degree position. This is to ensure that power from the driver gear is transmitted smoothly to the driven gear. Applying my knowledge of turning moments and cantilevers, I redesigned my motor stand such that the vertical arcyllic section is screwed to the 3D printed base section.
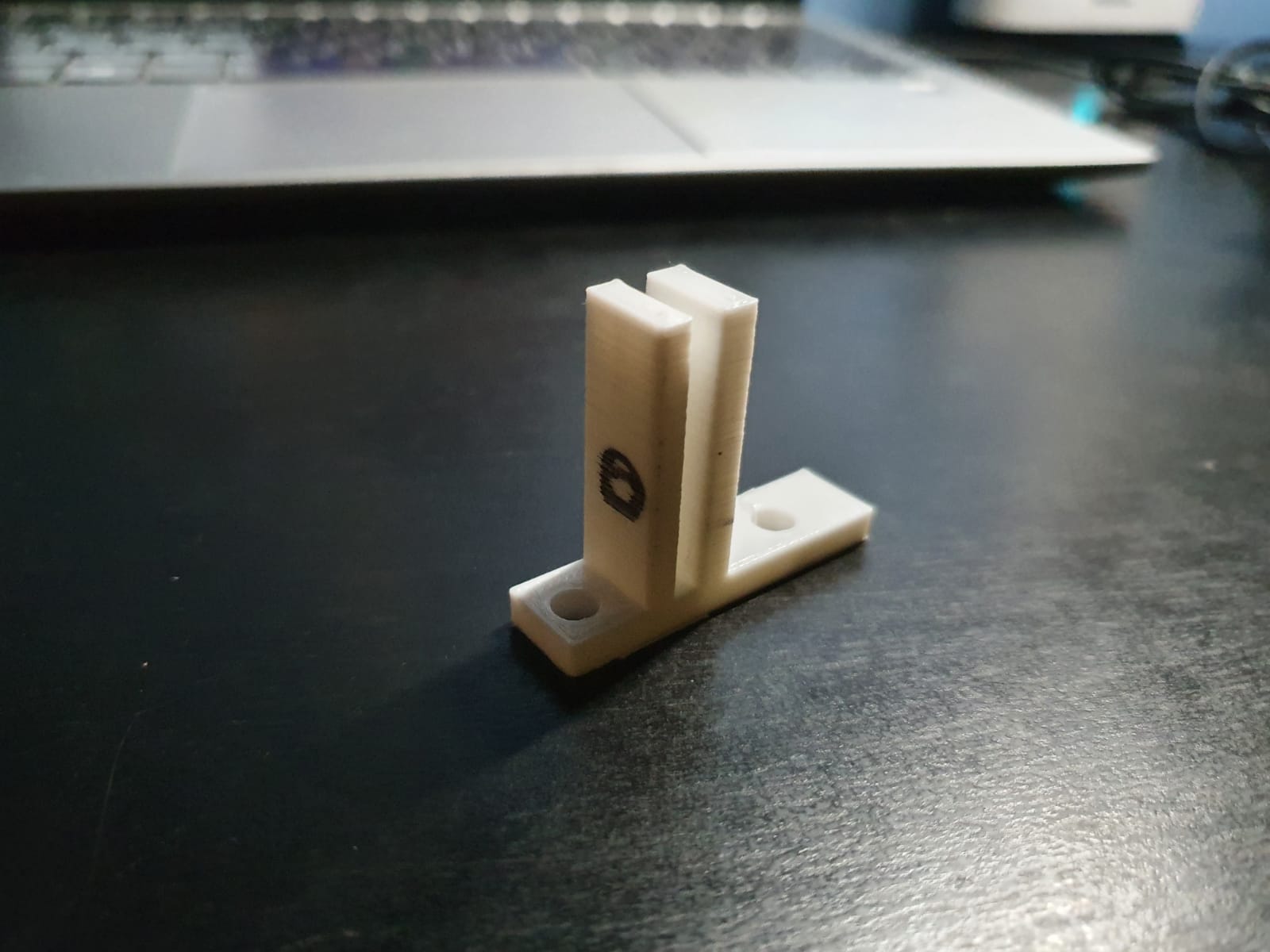
This is my original design but I re-3D printed such that there is a hole in the vertical section.
2. The second challenge I face was a reliability issue. The original movable cover was not reliable due to the mechanics. Despite programming the motor to run at full step (highest torque), the movable cover had difficulty moving in the upwards direction whilst it had little difficulty moving downwards as it is assisted by gravity. Owing to my basic knowledge of Second Moment of Area that I learn from my Mechanics module, I knew I had to reduce the weight of my movable cover. Hence I re-3D printed the movable cover such that there is a hole in the center and I covered the hole with a translucent plastic sheet. The translucent plastic sheet does not only perform its purpose to cover the hole, it adds to the artistic aspect of my design as well. Furthermore, I redesigned my movable cover such that the driven gear attached to it has a larger thickness. This will further boost the torque carrying capacity of the driven gear.
3. Another obvious but easy challenge I had was friction between the moving parts. I overcame this by applying lubricant around the hinges and in between the moving gears. I used Vaseline to lubricate the parts.